隨著新興市場經濟和新技術的興起,企業(yè)迫切需要生產高質量、低成本的產品。然而,近年來,在國內現有生產條件下生產的產品存在許多問題。
傳統(tǒng)意義上,生產需要設備處于恒定的工作狀態(tài),以便隨時檢測。但這種工作模式導致設備閑置一定時間的現象,極大地浪費了生產資源,無法實現可靠的自動化生產。
還有一個更重要的原因是,對于工業(yè)生產線上生產的產品,大多數人都是用自己的主觀意識或者淺薄的檢測方法來判斷零件的尺寸是否合格,這種判斷方法檢測出來的精度根本無法滿足客戶的需求。
基于上述問題,基于機器視覺的檢測方法應運而生,給生產加工行業(yè)的自動化和智能化帶來了前所未有的變革。
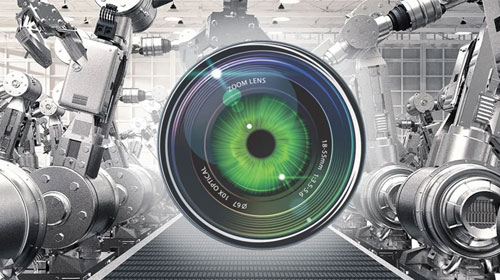
隨著機器視覺的應用,機器視覺的應用大大提高了產品質量,減少了人口紅利,在一定程度上降低了生產成本,帶動生產加工行業(yè)走向自動化、智能化的道路。
機器視覺定位
系統(tǒng)的總體結構
基于工業(yè)生產線上不同零件尺寸的檢測,機器視覺對零件尺寸的檢測主要分為三個部分:圖像采集、圖像分析處理、顯示結果和控制。
該系統(tǒng)主要由電腦主機、工業(yè)攝像機、LED光源和光電傳感器、PLC可編程控制器、單片機控制器、黑匣子等組成。
工作過程如下:首先設備初始化自檢,然后電腦主機通過軟件驅動工業(yè)相機(面陣CCD傳感器),但此時工業(yè)相機只是處于等待采集圖像信號的狀態(tài)。當光電傳感器沒有檢測到物體時,此時工業(yè)相機繼續(xù)等待采集圖像信號;當光電傳感器檢測到產品經過時,開啟LED光源并觸發(fā)工業(yè)相機采集零件的數字圖像信號,然后關閉LED光源。單片機控制器通過USB串行通信將數據傳輸到上位機進行圖像處理。圖像處理后,判斷物體是否合格,放入不合格品收集箱,合格則檢測下一個產品。